Ceramic Nitride Materials: New Routes and Applications
Our current interests in this area evolved from a "Materials Through Chemistry" effort that began in our group in 1985. That program centered on the preparation of inorganic preceramic polymers that could be used to form ceramic materials in non-traditional (non-powder) forms. At the time, large international efforts were in progress to prepare silica, silicon carbide and silicon nitride precursors, but little attention was being devoted to non-silicon preceramic materials. Stimulated by specific potential applications for boron nitride, our group, in collaboration with Riley Schaeffer and Sandia National Laboratory staff, undertook a program to develop preceramic precursors for BN. That program was highly successful and much of the work has been summarized in reviews (Chem. Rev. 1990, 90, 73; J. Inorg. Organomet. Polymers, 1992, 2, 183; Chemtech. 1994, 29; ACS Symp. Ser. 1994, 572, 358). The main theme centered on the preparation of poly-(borazinylamine)oligomers that were then used to form preceramics in fiber, xerogel, aerogel, aerosol and coating forms. Each was thermally transformed to boron nitride while preserving the non-powder forms. Except for BN fibers that were reported prior to our discoveries, the other BN forms were unique at the time and their potential applications attracted significant attention from ceramic producers. With the attention came many requests for samples that typically arrived as: "Could you send us a pound or two for evaluation by our scientists and engineers?" Unfortunately, these requests revealed a short-coming in our approach: the borazene monomers used in our syntheses were commercially unavailable, air sensitive, expensive to prepare, and difficult to prepare. In short, these great precursors were not amenable to commercial production. As a result, a "Valley of Death" appeared between our fundamental research advancements and the practical applications.
The realities surrounding preceramic polymers for BN led us in the late ‘90s to explore other, less expensive options for the formation of BN in non-traditional forms that would display some of the unique properties and applications found in the preceramic polymer work. In one case, Dave Lindquist in his Ph.D. studies observed that poly-(borazinylamine) dissolved in liquid ammonia and the resulting solutions could be used to form a preceramic polymer aerosol. Pyrolysis of the aerosol droplets led to the isolation of BN powders that contained primary particles with a spherical morphology as opposed to the standard platelet morphology formed by BN as a consequence of its layered hexagonal crystal structure. A spherical form of BN was of interest since such powders should pack more efficiently than platelets giving rise, for example, to more highly loaded ceramic particle/organic polymer composites. The polymer/aerosol synthesis, however, produced only low yields of these unique powders. Was there an alternative approach that did not require the expensive polymers?
The next attempts to produce significant quantities of spherical BN were based upon one of the standard commercial syntheses of traditional BN powders namely a high temperature reaction between boric acid and melamine and/or urea. Homogeneous aqueous solutions of these reagents were used to form aerosol droplets that were then passed through a horizontal flight tube in a stream of nitrogen heated to > 1000 °C. Unfortunately, the initial results were completely unpromising as all that seemed to take place was dehydration of the boric acid. Continued efforts led to the discovery that the direct reaction of aqueous aerosols of boric acid with gaseous ammonia at temperatures 900 °C – 1500 °C led to the formation of spherical powders of composition BNxOy where the values of x and y were dependent upon several experimental parameters including reactor tube temperature, gas flow rates and the NH3/N2 gas mole fraction. The powders obtained were then subjected to a second static pyrolysis under ammonia that resulted in complete nitridation and formation of dense, spherical morphology BN powders or completely transform to blades (see SEMs below). With addition of crystallization aides, the smooth spherical particles could also be induced to form distinct blades on the surface (Chem Mater. 2000, 12, 19; U.S. Pat. 5,204,295, April 20, 1993) (see SEM at far left, below). In addition to the studies with boric acid-based aerosols, a joint study with D. Schubert and D. Visi at U.S. Borax revealed that several commercial polyborates could be used as water soluble boron precursors in an aerosol production of BNxOy particles (Chem. Mater. 2005, 17, 2005). Related aerosol processing was extended to the formation of AlN, GaN and InN spherical particles (Chem. Mater. 2001, 13, 12).
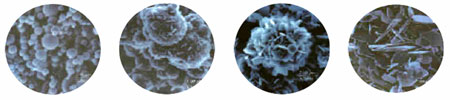
The new aqueous based aerosol processes that employed inexpensive inorganic feedstocks such as H3BO3, Al(NO3), Ga(NO3)3 and In(NO3)3 offered a huge benefit in cost and production rate over polymer or organometallic precursors used previously, but the systems still faced drawbacks especially for large-scale production of BN. In this case, it was clear that higher process temperatures were required for B-O bond nitridation and these higher temperatures were driving a back-reaction between the intermediate BNxOy particles and water. (steam). This led to a search for inexpensive precursors that could be utilized without water.
Alkyl borates, (RO)3B, with small alkyl groups are relatively low cost commercially available liquids. We found that these reagents, without solvent, form aerosols via ultrasonic agitation or spray techniques and subsequent reaction in an aerosol flight tube held at > 900 °C with ammonia generated BNxOyCz powders with spherical particle morphology (Chem. Mater. 2006, 18, 1434; U.S. Pat. 6,824,753, Nov. 30, 2004). Although carbon was found at low % weight levels in these powders, its presence assisted the subsequent removal of oxygen via a carbothermal reduction reaction. In addition, the amount of oxygen in these powders was overall much lower than present in the powders formed from aqueous solutions of H3BO3. This facilitated the conversion of the BNxOyCz powders to BN during second stage calcinations under ammonia. In the absence of solvent, the production rates for spherical powders were more than 100 X that found in the aqueous systems and it is reasonable to expect that commercial production of spherical BN powders could be realized with the system. It is also noteworthy that the surface nanostructure of these particles can be varied as shown in the SEM and TEM views shown below.
Very recently, Dr. Lynn Wood, during a summer sabbatical in the laboratory, discovered another interesting variant on the BN aerosol processing protocol. He found that use of H3BO3/DMF solutions led to formation of hollow BNxOyCz spherical particles. Such hollow particles have been observed in small numbers in some of our systems studied previously, but they were considered a nuisance since dense particles were the primary goal. Hollow particles seemed interesting, but without large amounts, their performance could not be characterized. With the new approach (Chem. Mater. submitted, U.S. Pat. App. ) it is now feasible to examine these particles in detail. Early findings reveal very low densities and high surface areas for the powders and gas adsorption properties are currently under study. A TEM of a sample of particles is shown here.
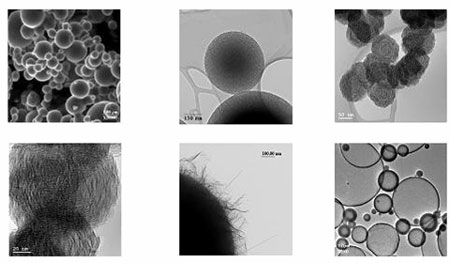
In addition to the above work, we are collaborating through a joint U.S./Polish program to explore the formation of metal nitride composites that may have useful optoelectronic properties. That work involves the group of Prof. J. F. Janik who has transferred the aerosol synthesis methodology to his group in Krakow (J. Phys. Chem. Solids 2004, 65, 639; Mater. Res. Bull. 2005, 40, 1136).